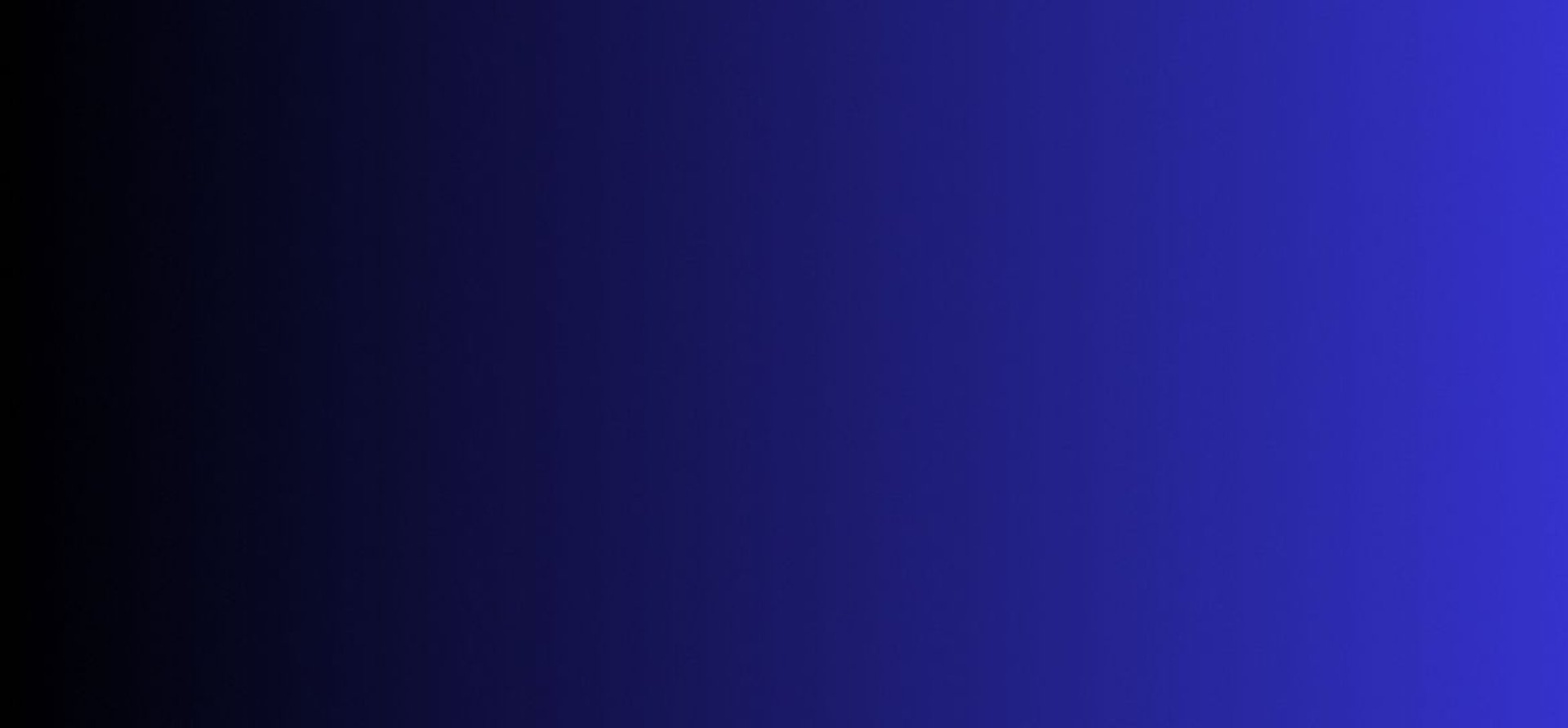
Master Tech skills on the go...
Integrating RFID and IoT for Workplace Automation
Discover how integrating RFID and IoT for workplace automation can enhance efficiency, boost productivity and improve security with practical, actionable insights.
DIGITAL PRODUCTIVITY & AUTOMATION
By OnlineTechSkills Editorial Team
5/10/20259 min read
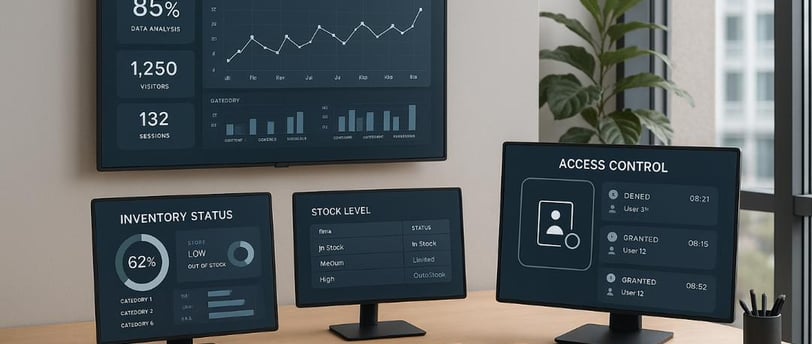
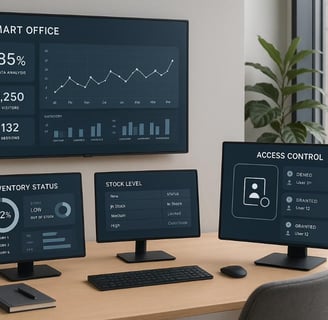
Introduction
Imagine walking into your office and having the lights, HVAC, and even the coffee machine spring to life the moment you badge in, no apps to open, no manual toggles. Or picture a warehouse where inventory levels adjust themselves in real time as items pass through a reader, automatically triggering reorder alerts or restocking robots. That’s the promise of marrying RFID (Radio-Frequency Identification) with IoT (Internet of Things).
In this deep dive, we’ll unpack how RFID tags, readers, gateways, and cloud platforms combine to make workplaces smarter, leaner, and more responsive. You’ll get practical tips, mini case studies, and pointers to tools and learning resources, so you can pilot your own automation project or add a lucrative service to your freelance toolkit.
Why RFID + IoT Equals Next-Level Automation
Most offices and warehouses rely on manual scans, clipboard checklists, or basic scanners that still need human input. By integrating RFID and IoT, you:
Eliminate human error. A tagged item is logged the moment it passes a reader, no miscounts or missing entries.
Enable real-time visibility. Stakeholders see asset locations, environmental conditions, or attendance as data streams into dashboards.
Trigger automated workflows. Low stock? Your ERP system automatically pushes a purchase order. Temperature spikes? You get an instant alert on Slack.
Boost security and compliance. Access control logs, audit trails, and credentials updates happen behind the scenes.
For entrepreneurs eyeing where to invest in upskilling, RFID and IoT fit right next to AI and cloud. If you haven’t yet scoped out the in-demand abilities for next year, check out Top 7 Tech Skills to Learn in 2025—No Experience Needed. It’s a quick tour of the core competencies employers crave.
Understanding the Building Blocks
Before we dive into architectures and code, let’s demystify the core components:
RFID Tags: Tiny transponders in labels or keyfobs. They can be passive (powered by the reader’s signal) or active (battery-powered for longer range).
RFID Readers: Devices that emit RF waves and capture tag responses. They range from handheld scanners to overhead portal readers in a loading dock.
IoT Gateways: Local hubs that bridge readers to the internet. They often support protocols like MQTT, HTTP, or CoAP, and handle encryption, buffering, and edge computing.
Connectivity: Wi-Fi, Ethernet, cellular, LoRaWAN, your choice depends on range, bandwidth, and power constraints.
Cloud Platform: Where data is stored, processed, and visualized. AWS IoT, Azure IoT Hub, or Google Cloud IoT come with built-in analytics, device management, and security.
Applications and Dashboards: Web or mobile apps often built with frameworks like Vue.js and Chart.js that turn raw reads into actionable insights.
Case study
1. Automated Inventory Management
Scenario: A small electronics refurbisher stocks dozens of components. Manual counting of resistors, capacitors, and circuit boards takes hours each week. Solution: Fit passive RFID tags to storage bins and mount readers at exit doors. When a bin is pulled for a build, the IoT gateway logs the departure. Your cloud dashboard updates in real time, triggers low-stock alerts, and sends reorder requests to suppliers.
2. Smart Access Control and Attendance
Scenario: A coworking space wants frictionless check-ins and accurate billing for meeting room usage. Solution: Issue active RFID cards to members. Readers at each room doorway record entries. The system invoices members monthly based on actual usage, and automatically revokes access for expired memberships.
3. Environmental Monitoring
Scenario: A pharma lab must maintain 2–8°C for vaccine storage. Temperature excursions risk spoilage. Solution: Place RFID-embedded sensor tags inside each fridge. Gateways transmit readings every minute to the cloud. If any tag reports out-of-range, IoT rules send SMS or Slack alerts to lab managers before hundreds of doses go bad.
These are just three examples. You can layer in AI for predictive maintenance (spot anomalies in reader logs), integrate with HR for automated onboarding, or tie in robotics for pick-and-place workflows.
Reference Architecture: From Tag to Insight
Let’s map the data journey step by step:
Tag Detection
Passive tag enters reader’s RF field.
Reader decodes tag ID and timestamp.
Edge Processing (Optional)
Gateway filters duplicate reads.
Simple business logic runs locally (e.g., ignore reads faster than X seconds apart).
Secure Transmission
Data packages sent via MQTT over TLS to cloud broker.
Cloud Ingestion
Messages land in an IoT backend; AWS IoT Core, Azure IoT Hub, or Google Cloud Pub/Sub.
Stream Processing and Storage
Use a serverless function (Lambda, Azure Function) or Stream Analytics job to enrich data (add GPS, user info).
Store in a time-series database like InfluxDB or a document store like DynamoDB.
Business Logic and Automation
Event triggers: low stock, access violation, temperature breach.
Invoke workflows in Zapier, Make, or a low-code tool, learn how to choose in IFTTT vs Zapier vs Make: Which to Use When.
Visualization and Reporting
Dashboards built in Grafana, Power BI, or a custom web app (Vue.js + Chart.js).
Automated email or Slack reports on key metrics.
This architecture scales from a dozen tags to thousands, no forklift upgrades needed.
Hardware Selection: Tags, Readers, and Gateways
Choosing RFID Tags
Range Needs: Passive tags read at 10cm to several meters; active tags can hit 100+ meters.
Durability: For industrial settings, use rugged tags rated for temperature extremes and moisture.
Form Factor: Labels, wristbands, keyfobs, or glass-encased tags for harsh environments.
Picking Your Readers
Fixed vs. Handheld: Fixed mount for portals or workstations; handheld for spot checks and audits.
Protocol Support: Look for readers with MQTT or HTTP APIs if you want direct cloud connections.
Antenna Configuration: Multiple antennas on a single reader can cover wide aisles.
Selecting an IoT Gateway
Edge Compute: Gateways with Node-RED support let you prototype logic without writing firmware.
Connectivity Options: Ethernet + Wi-Fi for offices; cellular or LoRaWAN for remote sites.
Security Features: TPM modules or hardware encryption for enterprise compliance.
If you’re exploring AI-driven analytics on your collected data, see How to Use AI for Data Analysis and Insight for prompts and techniques to mine patterns from your IoT streams.
Prototyping Your First System
Ready to build? Here’s a 6-step game plan:
Define the Scope
Choose one process, inventory pick, room access, or environmental check.
Set clear KPIs: reduce counting time by 80%, eliminate fridge alarms, or cut unauthorized entries.
Gather Hardware
Pick a handful of tags, one reader, and a gateway.
For hobbyist budgets, off-the-shelf dev kits from Impinj, ThingMagic, or Nordic/Arduino with an RFID shield work well.
Configure the Reader
Connect via Ethernet, assign a static IP, and point its data output at your gateway or local broker.
Test reads with sample tags, note how often duplicates appear.
Build a Simple Edge Flow
Launch Node-RED on the gateway.
Consume incoming tag messages, filter duplicates, and forward unique events to your cloud endpoint.
Cloud Setup
Spin up a free tier AWS IoT Core instance (or Azure/Google equivalent).
Define a rule to route messages into a DynamoDB table or CloudWatch Logs.
Dashboards and Alerts
Use Amazon QuickSight or Grafana to visualize reads per minute, top tags, and error rates.
Configure an alert on read failures or missing data windows.
With that minimal viable prototype, you’ve validated your core use case. From here, iterate on reliability, add security, and expand your hardware fleet.
Automation and Integration Best Practices
Linking RFID + IoT data to your existing business tools is where the real ROI lives. Here are top tips:
Use Webhooks or MQTT Triggers Send a webhook to Zapier or Make when a tag read meets a condition. Zapier can then create a row in Google Sheets, post to Slack, or call a REST API.
Embrace Low-Code Workflows Tools like Workato let you embed conditional logic “If stock < 10, then send an Outlook email to procurement.” Learn more in Automating HR Onboarding Processes with Workato: A Comprehensive Guide. Although that guide focuses on HR, the same patterns apply to inventory or security alerts.
Centralize Your Rules Engine Rather than sprinkling logic across Lambda functions, consider an open-source rules engine (like Drools) or a service like AWS IoT Events. You maintain one repository of business logic for temperature breaches, asset-moving, and access logs.
Version Control for Configurations Store your Node-RED flows, Terraform scripts for IoT resources, and automation recipes in Git. This practice pays dividends when you audit changes or roll back a faulty update.
Data Management and Analytics
RFID + IoT solutions generate torrents of time-series data. Tame the flood with these strategies:
Choose the Right Store
High-frequency tag logs → time-series database (InfluxDB, AWS Timestream).
Enriched events with metadata → document store (MongoDB, DynamoDB).
Implement Data Aging Policies Keep raw data for a sliding window (30–90 days) then roll up to summaries (reads per hour) for long-term storage.
Run Batch and Stream Analytics
Stream: flag anomalies in real time (e.g., sudden read drop).
Batch: generate nightly reports on asset utilization trends.
Visualize Wisely Dashboards should spotlight actionable metrics:
Critical: Stock levels, environmental alarms, unread tags.
Overview: Daily read volume, top 10 mobile assets, average dwell time.
If you’re ready to build custom dashboards, our guide on How to Create Dynamic Dashboards with Vue.js and Chart.js shows you how to wire live IoT data into responsive charts.
Security and Privacy Considerations
Automation must not compromise security or user privacy. Keep these practices front and center:
Data Encryption Enforce TLS between readers, gateways, and cloud services. For active tags, consider AES-128 encryption on the RF link.
Access Control Implement role-based access on your dashboards. Only supervisors see sensitive logs; operators get limited views.
Tag Privacy Avoid embedding personal information in RFID tags. Instead, store minimal IDs on the tag and link to user data in a protected database.
Compliance If you operate in GDPR or HIPAA jurisdictions, map data flows, record processing activities, and provide data removal options for individuals.
Physical Tamper Detection Seal readers in lockable enclosures and log any removal or power outages for audit trails.
Security is the foundation that lets you scale automation without risking data breaches or regulatory fines.
Integrating AI and Prompt Engineering
RFID and IoT supply the raw data; AI turns it into foresight. Consider these integrations:
Anomaly Detection Models Train a simple autoencoder or Isolation Forest on normal read patterns. When the model flags an unusual drop in reads (which might indicate reader failure), you get a proactive alert.
Predictive Maintenance Tag-reader connectivity logs can reveal reader hardware degradation. Feed metrics like read latency or error counts into a regression model that predicts failure before it happens.
Natural-Language Queries Instead of hacking dashboards, ask an AI assistant: “Show me days last month when fridge temperature exceeded 8°C for more than 15 minutes.” Use prompt-engineering tactics from A Beginner’s Guide to Prompt Engineering with AI Tools to craft precise, actionable queries.
Automated Report Generation Send weekly summaries “Total reads per zone, five highest-traffic assets, three critical alerts” via ChatGPT or Claude. Learn how to train your AI assistant for business tasks in How to Train Claude AI to Act Like Your Business Assistant.
By layering AI atop your IoT streams, you shift from reactive firefighting to strategic foresight.
Getting Started as a Freelancer or Entrepreneur
RFID + IoT integration is a hot niche. Here’s how to position yourself:
Define Your Service Offering
Hardware procurement and setup.
Edge logic and gateway configuration.
Cloud ingestion, analytics, and dashboard build.
Workflow automation (Zapier, Workato).
Assemble a Basic Demo Kit Show prospects a live prototype: tagged assets, a reader scanning them, and a dashboard updating in real time. A shiny demo rather than a slide deck wins trust fast.
Package Your Expertise Create a landing page with case studies: “We cut warehouse cycle counts from 4 hours to 15 minutes.” Outline your process, from consultation to support.
Upskill Continuously Learn the latest IoT platforms and RFID hardware. For structured learning, explore Best Online Platforms to Learn Practical Tech Skills in 2025.
Network in Niche Communities Join RFID and IoT meetups on LinkedIn or Slack communities. Share troubleshooting tips, ask about tough deployments, and stay on the cutting edge.
Skills Roadmap and Resources
Whether you’re pivoting into IoT or adding automation to your freelancing arsenal, these resources will guide you:
Core Tech Skills Embedded systems basics, MQTT/HTTP protocols, cloud functions. More ideas in The Fastest-Growing Tech Careers You Can Start from Scratch.
Front-End Dashboards Vue.js and Chart.js for real-time visuals, see Roadmap: How to Become a Front-End Developer in 90 Days.
AI and Data Analysis Training anomaly detection models, building NLP prompts, start with AI-Powered Learning: How to Use ChatGPT as a Personalized Coding Tutor.
Automation Platforms Compare IFTTT, Zapier, Make, and Workato: which one suits your orchestration needs? Learn in IFTTT vs Zapier vs Make: Which to Use When.
These guides help you assemble the perfect skill set for delivering end-to-end RFID + IoT solutions.
Future Trends: What’s Next in Workplace Automation
RFID + IoT is already transforming industries, but the next wave is even more exciting:
5G-Enabled Readers Ultra-low latency, high throughput for video-tag correlation.
Digital Twins Virtual replicas of physical assets, updated in real time as tags move.
Edge AI Running lightweight ML models directly on gateways for split-second decision making.
Blockchain for Supply Chains Tamper-proof records of RFID events across multiple stakeholders.
Sustainability Tracking Monitoring energy usage, carbon emissions, and waste in real time.
Remote and hybrid workplaces will lean on these innovations to keep operations agile and resilient, learn more in The Future of Work: Trends in Remote and Hybrid Employment.
Action Steps: Launch Your First Pilot
Pick a High-Impact Use Case Inventory, access control, or environmental monitoring, start small.
Gather Demo Hardware Order a reader, a dozen tags, and an IoT gateway dev kit.
Follow the Prototyping Steps Build edge flows, connect to a cloud IoT service, and spin up a basic dashboard.
Automate a Workflow Use Zapier or Workato to send a Slack alert or create a purchase request when a condition triggers.
Measure and Iterate Track time saved, error reduction, and stakeholder satisfaction. Refine your solution before scaling to other areas.
Within a few days, you’ll have a live proof of concept and the confidence to pitch larger automation projects.
Conclusion
Integrating RFID and IoT isn’t about adding more complexity. It’s about stripping away manual steps, reducing errors, and making data flow effortlessly so your team can focus on strategic work. From frictionless check-ins to self-ordering warehouses, the possibilities are vast and open to anyone willing to prototype, iterate, and learn.
Whether you’re a freelancer building a new service line or a tech leader streamlining operations, these principles and tools will guide your journey. Grab a dev kit, pick a use case, and start automating. The future of work is live data and seamless workflows and it begins with a simple RFID tag.
Insights
Explore our free and top ranking blogs for in-demand tech skills.
CONTACT US
Support
support@onlinetechskills.com
© 2025. All rights reserved.